I. Introduction
Plastic pollution is considered one of the major environmental issues in the world today. More and more plastic waste disposal issues come along with the increase in plastic product production and consumption. In the face of such a situation, plastic crushers efficient, plastic processing waste equipment gradually become the main tool for the plastic recycling industry. This article is going to in-depth research the types of plastic crusher machines, their working principles, selection guidelines, and the roles they play in the environment and the economy.
II. What is a plastic crusher?
A plastic crusher is a machine specifically meant for smashing plastic waste into smaller pieces; it cuts solid plastic materials into small pieces easily handled by using high-speed rotating blades, thus creating favorable conditions for subsequent recycling and reuse. Plastic crusher machines can be used to crush plastic bottles, packing materials, or industrial plastic waste—any of them.
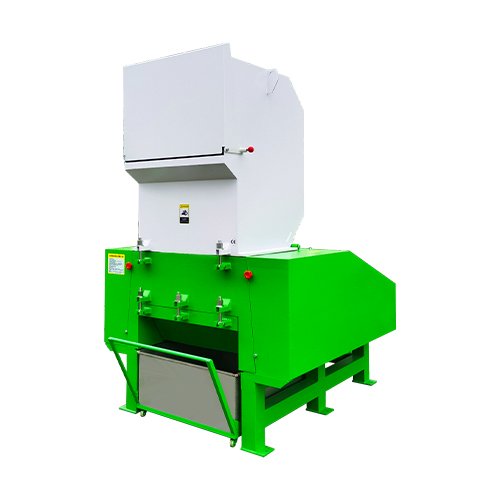
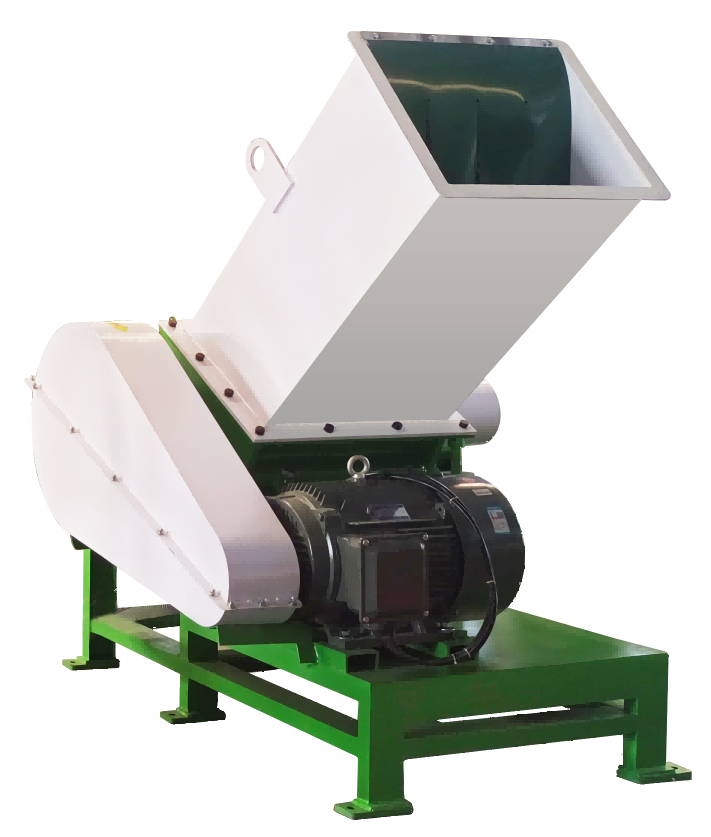
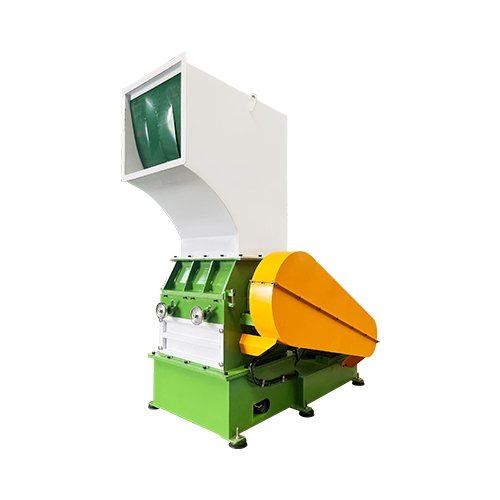
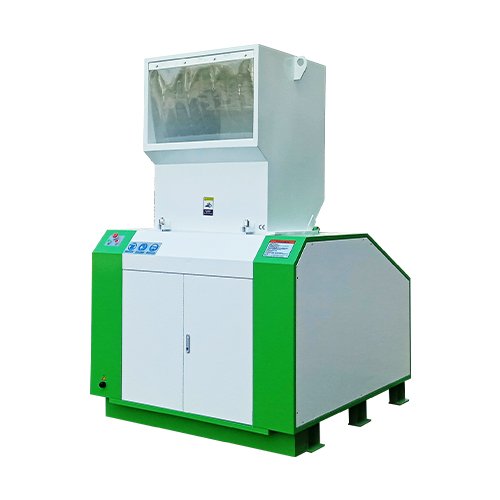
1. The Core Working Principle of Plastic Crusher
Plastic crushers work on a principle that involves the physical cutting and crushing of plastics. Once the plastic waste is fed into the crushing chamber, the blades rotating at a very high speed first cut the material, after which the material is broken into smaller granules. The size of the final fragments can further be controlled by the diameter of the screen perforations or by adjusting the blade configuration to meet specific recycling process requirements.
2. Detailed description of working mechanism
The plastic crusher machine has parts – motor, group of cutters, transmission system and screen.
The motor makes the group of cutters rotate fast. A cutter group comprises a set of blades, which include fixed as well as movable knives. Plastic products enter the hopper of the crusher from where they are fed into the cutter group. These blades inside the cutter group rotate at a high speed; the cutting force of the cutter group will make the plastic products break. At the same time, the high-speed rotating blades will also impact and shear the plastic products; this way, the pulverization process will further be accelerated. Cutting, impacting, and shearing, the plastic wares are cut into minute particles or fine powder. The crushed plastic particles or powder are fed into the screen as the group of cutters rotate. The screen is used to control the size of the pulverized material required. By setting different apertures of screens, the size of the pulverized particles can be controlled. The screen will block larger particles and they will circulate and pulverize inside the crusher; this will continue until the desired pulverization effect is achieved.
3. Role of the Transmission System
Besides these, the plastic crusher has a transmission system by which the motion or power of the motor is transmitted to the group of cutters. Normally, the system of transmission consists of pulleys, belts, etc. to make sure that the group of cutters rotates at a high speed. This design allows the crusher to properly work on all different kinds of hard and soft plastic waste. The stability and strength of the transmission system most likely will have a direct impact on the total performance and the service life of thecrusher.
III. Key Components and Functions of Plastic Crusher
A number of key components are making up plastic crushers that play a critical role in the performance and efficiency of the whole machine. These are:
1. Blade
Normally, the core part of the crusher, this is made of tungsten steel or carbide, capable of bearing high-intensity cutting tasks. Design and arrangement will be done according to the type of plastic processed and the size requirement of the final fragments.

2. Hopper
The hopper guides plastic waste material into the crushing chamber. Some hoppers come with either agitators or screw propellers, which further provides uniform feeding of material into the machine.
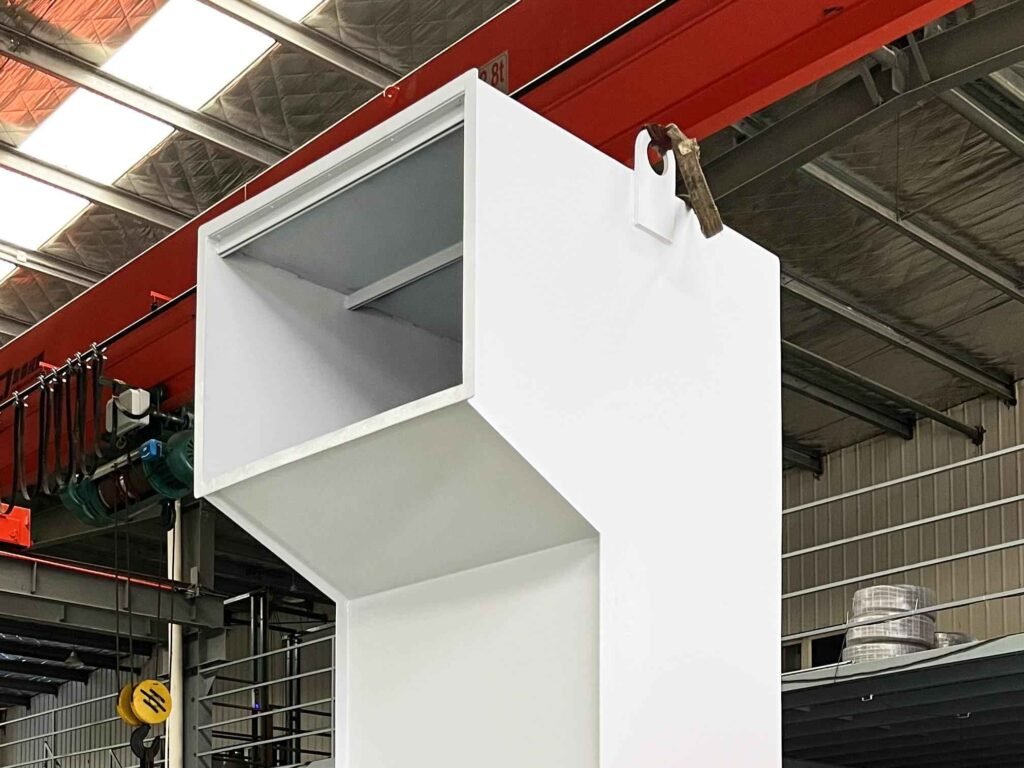
3. Screen
It is positioned just below the blade and serves to manage or control the size of fragments; only those smaller than its aperture size can pass hence ensuring the uniformity of the output.
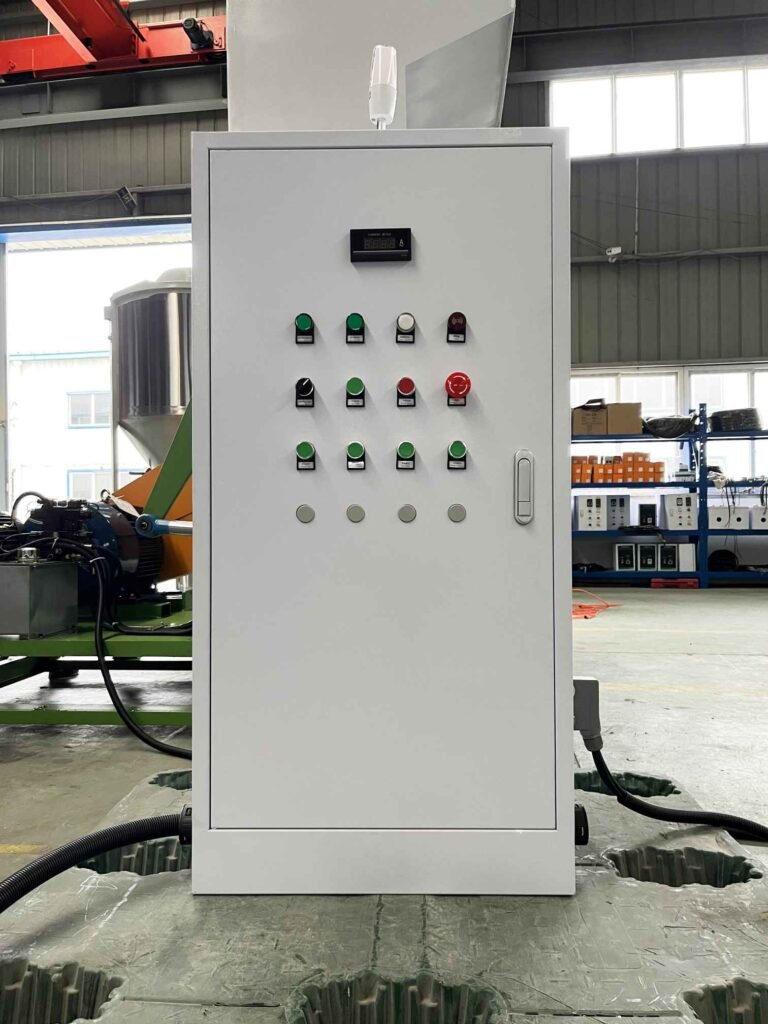
4. Casing
It is the outer covering of the apparatus, used for guarding the internal parts and enabling safe functioning. Drive system gives power to the crusher, normally by an electric motor or diesel engine to make sure that the machine can work well.
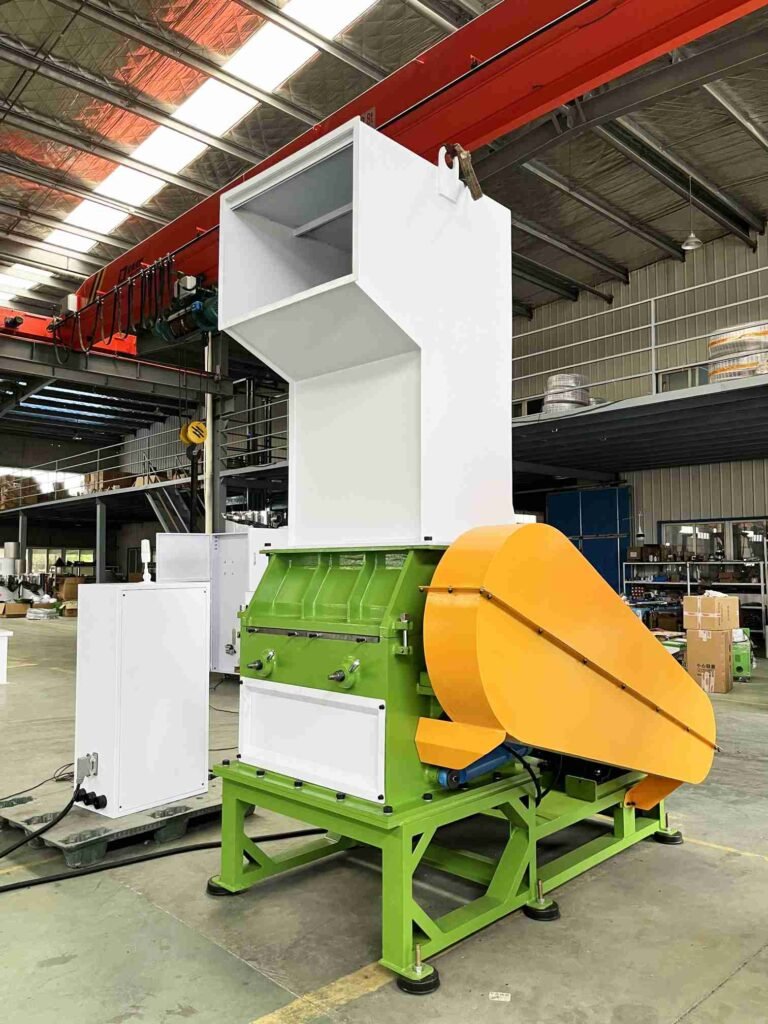
IV. Types of plastic crushers
1. Single-shaft plastic crushers
Single-shaft plastic crushers happen to be the most popular type of plastic-shredding equipment; the plastic is cut into small pieces by the blades of the rotating single shaft at a very high speed. It is applicable to small and medium plastic waste, more particularly when fine crushing is necessary, like in the production of plastic pellets or in the processing of film waste. Operation of single-shaft plastic crushers is relatively simple; hence, the machines have low costs of maintenance, which makes them ideal for small recycling plants and laboratories.

2. Double-shaft plastic crushers
Double-shaft crushers have double shafts that rotate in opposite directions and have the capacity for large volume plastic waste. Most likely, this machine finds its use in industrial recycling and has no challenges in smashing huge plastic materials such as plastic pallets, pipes and big containers. The product of a double-shaft crusher normally includes pieces or flake plastics, ready for the next process. Owing to its double-shaft structure, it has evident advantages in dealing with large plastic material of irregular shape to further enhance the efficiency and quality of crushing.
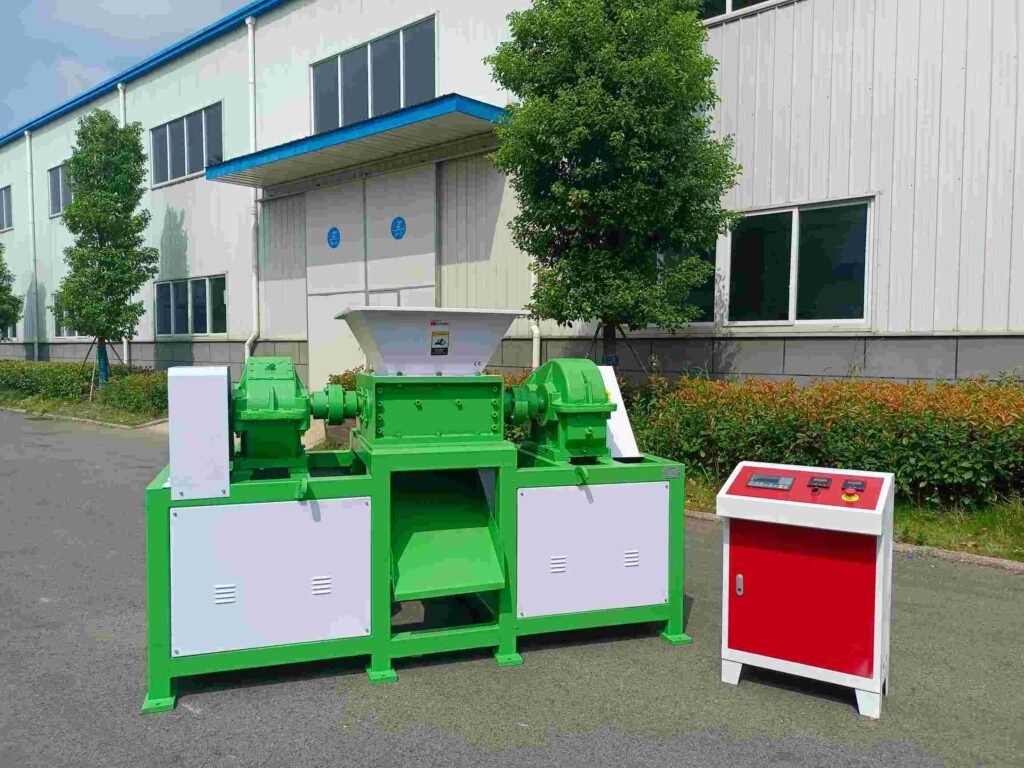
3. Four-axis crusher
The four-axis crusher is heavy machinery meant for extremely tough crushing tasks—for instance, of large wood, rubber, and thick plastic. It achieves high crushing capabilities by the cooperative action of four axes and is mostly applied in construction waste and industrial waste processing. Material of very high hardness and toughness can be dealt with using the design of the four-axis crusher; it is apt for processing heavy waste.
4. Granulator
The granulator is only but one machine that is purposed for processing plastic waste into uniform particles. It cuts the plastic into 6-50 mm particles by means of screens and blades – particles that can be directly used in making new products. Granulators find wide applications in the plastic recycling industry, more especially in those production processes demanding the presence of particles of high precision. Its fine crushing and screening functions ensure the quality as well as the consistency of the final product.
5. Grinding machine
Normally, the grinding machine produces plastic waste powdered to dimensions of 2 to 8 mm. That is commonly applicable to the production process of composite materials and injection molding. In easier terms, the plastic waste is turned into relatively higher value raw material. The grinding machine makes the powder fine and uniform after it goes through several grinding and screening processes. It seems applicable for industrial applications that are highly demanding.
6. Hard Plastic Crusher
Hard Plastic Crusher is suitable for crushing various small and medium-sized plastic sheets, such as ABS, PE, PP sheets, etc. This crusher uses sealed bearings to ensure that the bearings run well for a long time. The knife type design is reasonable, the product is evenly granulated, the knife seat has been heat-shrunk, and the appearance design is beautiful and generous. The rectangular feeding port of the hard plastic crusher is convenient for the input of long strips of sheets, improving work efficiency. Suction fans and storage barrels can be optionally equipped to form a sheet crushing and recycling system to give full play to the recycling efficiency.
8. Powerful Plastic Crusher
The sheet knife structure of the powerful plastic crusher is between the claw knife and the flat knife, which is suitable for crushing ordinary sheets, pipes, profiles, sheets and packaging materials and other plastic products. This crusher uses sealed bearings to ensure that the bearings run well for a long time. The knife type design is reasonable, and alloy steel blades are used to crush the product evenly. The knife seat has been heat-shrunk and strictly balanced to ensure stable operation of the machine and beautiful appearance design. The powerful plastic crusher is suitable for crushing a variety of plastic products, with wide applicability and high efficiency.
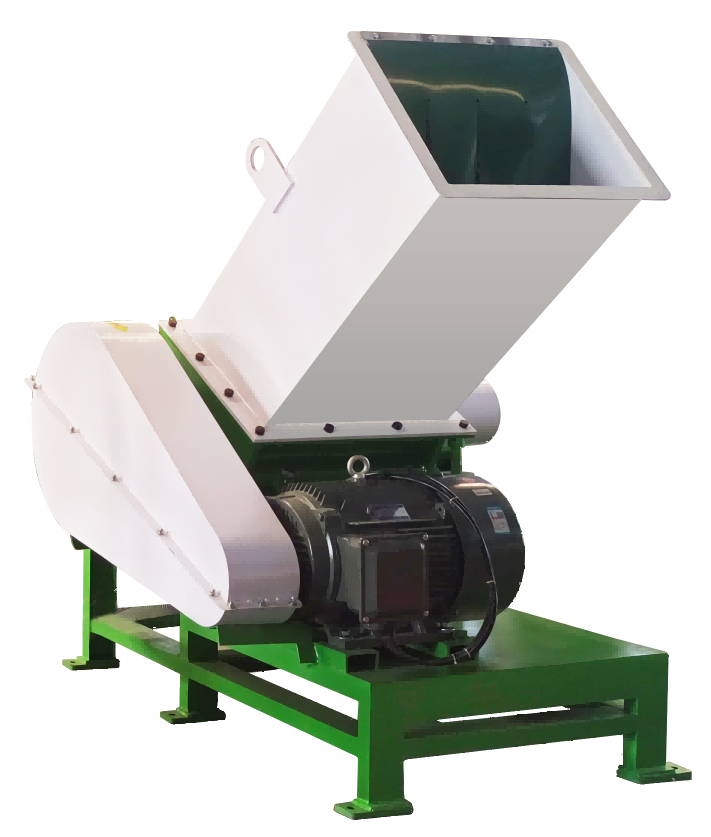
9. Plastic pipe crusher
Plastic pipe crusher is suitable for crushing various small and medium-sized plastic pipes, such as PE, PVC pipes, silicon core pipes, etc. This crusher is designed with a round tube feeding port for crushing pipe materials, which is convenient for the input of long pipes and improves work efficiency. Suction fans and storage barrels can be optionally equipped to form a pipe crushing and recycling system to give full play to the recycling efficiency. Sealed bearings are used to ensure that the bearings operate well for a long time; the knife type is reasonably designed and the product is granulated evenly; the knife seat is heat-shrinked and the appearance design is beautiful and generous. The plastic pipe crusher performs well in handling pipe waste and is an ideal choice for pipe recycling.
V. How to safely operate and maintain the plastic crusher
1. Safety operation guide
(1) Preparation before operation: Before starting the plastic crusher, you should first move the drive wheel one or two circles by manpower, and confirm that the movement is flexible before starting the plastic crusher. Wait until the plastic crusher is operating normally before starting to feed.
(2) Uniformity of feed: Keep the plastic crusher’s feed uniform to prevent overload. Prevent objects that cannot be crushed, such as metal and wood, from falling into the machine. When it cannot be crushed, the moisture content of the feed cannot be too high; when wet crushing, it is necessary to maintain an appropriate amount of water to prevent blockage due to insufficient flushing and reduce production capacity.
(3) Operation status monitoring: Pay attention to the operating sound of the machine at any time. Under normal circumstances, the operating sound of the crusher is stable and regular. If there is abnormal noise, such as sharp friction, collision or periodic “click” sound, it is likely that there is a problem with the internal parts of the machine, such as severe wear of the tool, foreign matter entering, etc., and it is necessary to stop the machine immediately for inspection.
(4) Cleaning after shutdown: Before stopping the operation of the plastic crusher, you should stop feeding and drain the material in the machine before cutting off the power supply of the motor. After the crushing is completed, the materials on the crusher hopper and the body should be swept out with a long-haired brush immediately, and the feed part of the crusher should be opened, and the crusher should be cleaned with wet linen or water.
(5) Personal protection: Pay attention to personal safety during the crushing process, do not wear too loose clothes, do not have long hair, and avoid accidentally rolling hair or clothes into the crusher.
2. Maintenance points
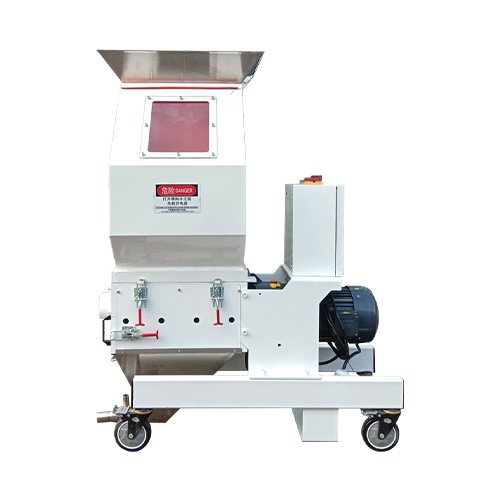
(1) Regular inspection and maintenance: Check the tool screws regularly. After using the new plastic crusher for 1 hour, tighten the screws of the moving knife and the fixed knife with tools to strengthen the fixation between the blade and the knife holder. Regularly add lubricating oil to the bearings to ensure the lubrication between the bearings.
(2) Tool maintenance: To ensure the sharpness of the tool cut, the tool should be checked frequently to ensure its sharpness and reduce unnecessary damage to other parts caused by blunt blades. When replacing the tool, the gap between the moving knife and the fixed knife: 0.8MM is better for crushers above 20HP, and 0.5MM is better for crushers below 20HP. The thinner the recycled material, the smaller the gap can be appropriately adjusted.
(3) Cleaning work: After each use of the crusher, clean up the residual materials inside and outside the machine in time. For some materials that are easy to stick together, such as wet grass, fruit residues containing sugar, etc., they should be cleaned carefully to avoid the materials drying up and affecting the next use of the machine.
(4) Parts inspection and replacement: Regularly check the wear of the cutter (or crushing teeth). When the cutter is worn to a certain extent, it will affect the crushing effect and efficiency. According to the degree of wear, the cutter should be polished or replaced in time. The performance of the vulnerable parts of the machine, such as bearings, seals, etc., should be checked regularly. If the bearing is found to have abnormal heating, noise or inflexible rotation, and the seal has leakage and other problems, the corresponding parts should be replaced in time.
(5) Storage environment maintenance: Store the crusher in a dry and well-ventilated place. Avoid the machine from getting damp and rusting, especially for some crushers with metal parts. If the crusher is not used for a long time, anti-rust oil can be applied to the key parts of the machine, such as cutters, bearings, etc., and the machine can be covered with a dust cover to prevent dust from entering the machine.
Do you want to know more about how to use a plastic crusher? Just read this guide.
VI. How to choose a suitable plastic crusher
A suitable plastic crusher should integrate several aspects encompassing the type of plastic, processing volume, budget, and machine performance. The budget is quite a thorny issue as the average processing man cost can be calculated for involving how many kilowatts and processing how many tons; also, spare parts must be taken into account in the future cost. For a more detailed guide on how to choose a suitable plastic crusher, please refer to this article.

1. The impact of plastic type
Different plastics have different properties in terms of hardness and toughness and their chemical composition (melting point). For instance, low-melting plastics most probably will require a low-torque plastic crusher operating at high speeds, while high-hardness plastics, such as ABS and PC, will require heavy-duty equipment operating at high torques.
2. Processing capacity requirements
Choose a machine with the right capacity based on your production scale. Small recycling plants may only need a single-shaft plastic crusher, while large industrial recycling plants require dual-shaft or quad-shaft plastic crushers to handle large amounts of waste.
3. Budget considerations
Plastic crushers have a wide price range from a few thousand yuan to hundreds of thousands of yuan. The more high-performance equipment that is acquired has a larger initial investment cost, but the cost of running it for a long time is lower, and the return rate is higher.
4. Other selection factors
Machine size and footprint: Choose a machine size that fits your workspace.
Noise and environmental performance: Choose low-noise, low-energy consumption equipment as it is friendly to the environment.
After-sales service: Choose a manufacturer that gives full after-sales service, including technical support, supply of parts, and repair services.

VII. Conclusion
The plastic crusher is essential to the process of plastic recycling. It creates conditions whereby plastics can be reused and reduces environmental pollution to the lowest levels. The choice of plastic crusher should be executed based on the plastic type, processing volume, and budget, in addition to the safety and reliability of the machine. High-quality plastic crushers will work for small recycling plants as well as for large industrial applications and will for sure improve the working efficiency to a great extent which will lead to sustainable development.